GMPヒューマンエラー防止のための文書管理【第25回】
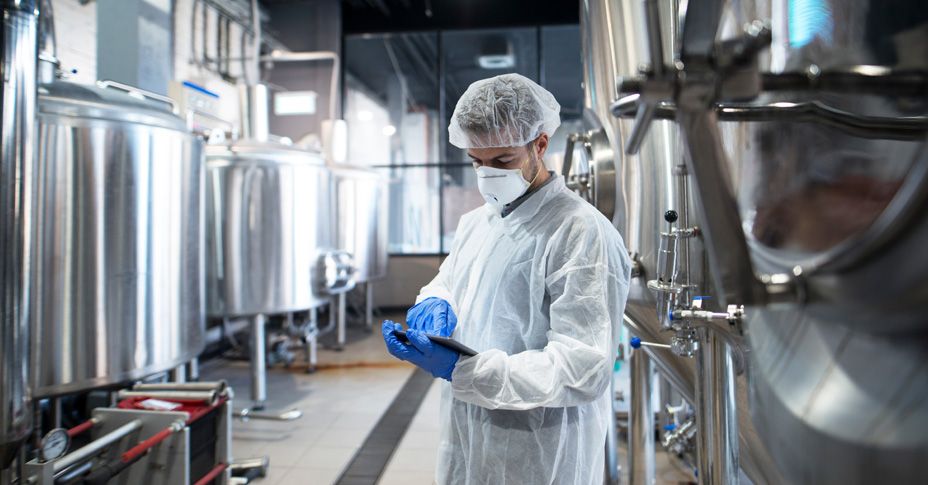
1.運用ができない手順
「手順書(SOP)がないと作業ができない。」との現場からの要望で、詳細な手順を記載することも多いことだろう。しかし、運用を開始すると、実際に手順書の記載どおりできないなどの文句が出ることもある。また、品質には影響しない「作業の逸脱」となることも多い。私の経験だが、文書管理規定に記録の修正方法を「1本線で見え消し」と規定していたところを「2本線で見え消し」で修正した箇所を監査で指摘されたことがあった。これを逸脱処理すべきであろうか。何も品質には影響はしないが、手順書からの乖離となる。本来、手順書(SOP)を作成する場合、その手順は、検証されていなければならない。PV(プロセスバリデーション)は、実生産において、その製造方法(手順)で製造すれば、期待する結果、つまり、品質に適合した製品ができることを検証することである。製造手順はバリデートされてから、手順書(SOP)の制定をすべきである。バリデーション実施時には、その製造方法を検証中のため、まだ、案の状態である。もし、バリデートされなければ、その製造方法(手順)は、適格性がないと判断しなければならない。手順書(SOP)は、検証されていなければならない。
バリデーションが実施できないプロセスもある。その場合は、リスク分析をして、手順のとおり行わないと、どんなリスクが発生するかを考えなければならない。考えられるリスクの低減策を図り、変更実施後に、想定したリスクの発生の状況とリスク分性をした以外のリスクの発生がないか確認することが必要である。リスクマネジメントで重要なのは、想定した以外のリスクが発生していないか、低減されたリスクが発生していないかを最終確認することにある。
手順書(SOP)を何も確認せず、いきなり作成して、運用することは却って無駄な作業をすることになる。急がば回れではないが、その手順で実際に行えることを試行することが必要である。試しもせずに行うのは無謀なことである。バリデーションを行えない場合、教育訓練として、試行することも一つの方法である。設備の洗浄は、洗浄バリデーションで確認するが、手洗浄する場合、実際に手が届くのか、分解が可能かなど、洗浄バリデーション以前に確認すべき点も多くある。回収処理の手順書では、その連絡体制が可能か、回収品の保管が可能かなどシミュレーションすることも重要である。実際に行えるかを模擬実験することで確認すべきである。災害対策としての避難訓練と同様に考えなければならない。手順書を制定し、いざ始めようとしたら、「こんなのできないよ」では話にならない。細部まで細かく規定している手順書(SOP)を作成すれば、作業者も理解しやすいかもしれない。しかし、品質に影響しないことまで規定することをGMPは求めていない。作業者が理解しやすく、プロセスが円滑に進むなら良いが、却って、作業の逸脱が増加し、非効率的になるのでは問題である。自分の首を自分で絞めることがないように手順書(SOP)を作成しなくてはならない。その為に、その手順が無理なく行えることを、制定前に確認することが必要となる。
GMPは、手順書(SOP)や指図に基づき作業することが基本である。しかし、手順書(SOP)を作業の傍らにおいて、読みながら作業をすることを求めているわけではない。品質に影響する重要な点は、その都度確認すべきであり、チェックをしたことも記録に残すべきであるが、すべての手順書を読みながら作業することは非効率的である。チェックの記録もすべてが必要ではなく、品質へ影響する項目で十分である。まずは、手順書(SOP)の制定前にその手順が実行可能なものかを検証することが重要である。GMPの基本は、ルール(手順書SOP)に従い、作業したことを記録することである。ルールのとおり作業できなければ逸脱となる。ルールを定める際に実行不可能では、ルールは守れないのである。実行できるルールを作るのが当然である。ここで、セミナーでよく使う次の「GMPの基本」スライドを見てもらいたい。コンサルタントの時、アシスタントがこのスライドに絵を入れてくれたのだが、GMPのセミナーで不適切だと思うと言ってしまった。
【問題】このスライドで不適切な部分はどこか。その理由は何か。
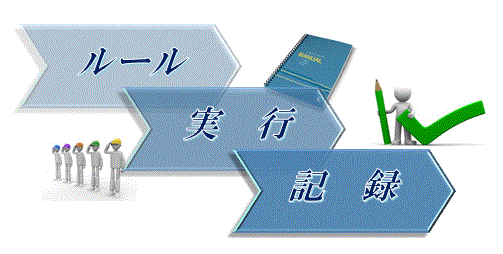
答えは次号に掲載します。
2ページ中 1ページ目
コメント
/
/
/
この記事へのコメントはありません。
コメント