GMPヒューマンエラー防止のための文書管理【第21回】
2019/06/07
品質システム
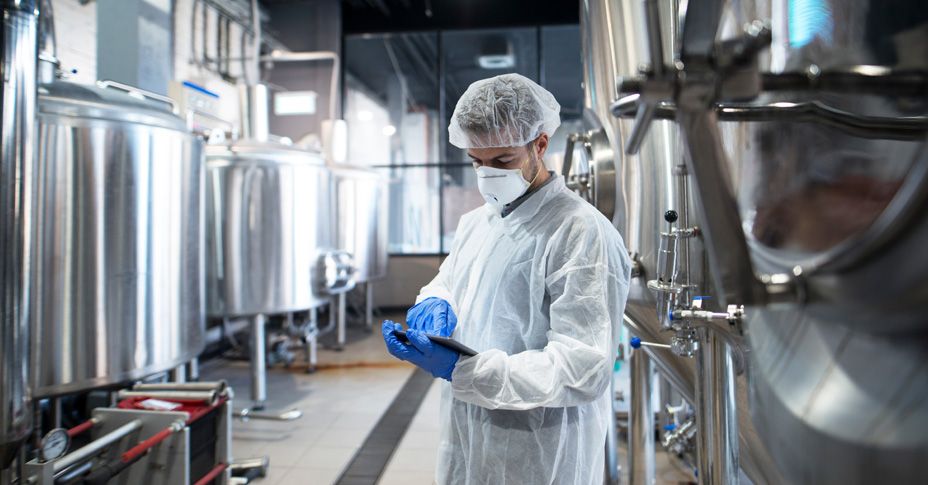
1.供給者管理
監査と査察を混同して使われる方も多い。査察は、いわゆる当局と呼ばれる審査機関や許可権者が行う調査で、GMP調査だけでなく、国税局査察部のことをマルサということをご存知の方も多いと思う。監査と査察の大きな違いは、その目的が違うことである。査察は、基本的に承認や許可のために確認する行為であり、査察官は、GMP省令等に違反する点がないかを調査し、審査する。適合することにより、承認等が付与される。監査は、契約や取り決めに反する行為がないかの確認である。日本では、お客様が一番の思想から監査等で指摘することは、必ず実施しないといけないと思われる方も多い。しかし、海外では、その点を取決めや製品仕様書に定めてなければ、聞いていないと主張される。輸入原薬商社に勤務していた時、錠剤の溶出性が今までと違うという事象が発生して、海外サプライヤーに確認したところ、粉砕機を変更したと回答があったことを経験した。その時、海外からの回答は、粒度についての規定は製品仕様書に定まってなく、求められていないので、その変更も連絡しなかったとのことであった。また、出発物質や中間体の変更で、類縁物質に変化があっても、規格内だからと、海外サプライヤーは変更の連絡をしてこないことも多い。取決め等は、どんな点が問題になるかリスク分析の上、締結しなければならない。しっかりとした取決めを締結するからこそ、監査が意味あるものになる。
GMP省令が改正され、供給者管理は、条文に明記される。今まで、施行通知に定められていた内容であり、指摘事項となっても、軽微で済んだが、今後は、メジャーの指摘となる。原薬についても、製造販売業者が監査しているはずだ、では済まされない。二重なチェックは不要だが、製剤製造所は、原薬製造所に関する情報を製造販売業者からしっかりと入手することが必要で、不足があれば、直接、監査することも必要となる。また、原薬製造所への監査において、原薬製造所が行う原料等の製造施設との取り決めや監査結果を確認することも必要である。原料が起因する異物や汚染を確認するには、現場の確認が必須である。直接の容器が原因で、安定性に影響することもある。吸湿性や遮光性も考慮することは当然だが、原薬や製剤バルクとして、保管する際に利用するポリ袋など、容器からの可塑剤等が滲出することもリスクとして考えるべきである。資材の組成は、社外秘で、開示されないことも多い。監査で確認すべきことは、製剤等の品質に影響する可能性の事象について、いかにして、確認するかである。当局の査察とは別の見方をしなければならない。
パッケージメーカーへの監査で、紙粉が多いと指摘しても無駄である。それより、大切なことは、印刷内容が適切に管理されていることや印刷に誤植やカスレなどがなく、適切に印刷されていることにある。この取り扱いもデータインテグリティの確保である。版の管理や印刷物のチェック方法も監査で見るべきポイントとなる。品質情報等を年次レビューして、リスク分析をしたうえで、監査を行うことが必要である。製造物により、監査の確認すべきポイントが変わるのは当然である。その点を踏まえて監査を行わないと、意味のない監査となってしまう。監査員は、その点を十分認識し、その製造する製品の品質を把握し、その工程での重要な点を理解し、最終製品へ与えるリスクが、その原料、資材の品質のどの点にあるかを考えて、監査をしなければならない。その場しのぎの重箱の隅をつつくような誤字脱字の指摘をしてはならない。
監査と査察を混同して使われる方も多い。査察は、いわゆる当局と呼ばれる審査機関や許可権者が行う調査で、GMP調査だけでなく、国税局査察部のことをマルサということをご存知の方も多いと思う。監査と査察の大きな違いは、その目的が違うことである。査察は、基本的に承認や許可のために確認する行為であり、査察官は、GMP省令等に違反する点がないかを調査し、審査する。適合することにより、承認等が付与される。監査は、契約や取り決めに反する行為がないかの確認である。日本では、お客様が一番の思想から監査等で指摘することは、必ず実施しないといけないと思われる方も多い。しかし、海外では、その点を取決めや製品仕様書に定めてなければ、聞いていないと主張される。輸入原薬商社に勤務していた時、錠剤の溶出性が今までと違うという事象が発生して、海外サプライヤーに確認したところ、粉砕機を変更したと回答があったことを経験した。その時、海外からの回答は、粒度についての規定は製品仕様書に定まってなく、求められていないので、その変更も連絡しなかったとのことであった。また、出発物質や中間体の変更で、類縁物質に変化があっても、規格内だからと、海外サプライヤーは変更の連絡をしてこないことも多い。取決め等は、どんな点が問題になるかリスク分析の上、締結しなければならない。しっかりとした取決めを締結するからこそ、監査が意味あるものになる。
GMP省令が改正され、供給者管理は、条文に明記される。今まで、施行通知に定められていた内容であり、指摘事項となっても、軽微で済んだが、今後は、メジャーの指摘となる。原薬についても、製造販売業者が監査しているはずだ、では済まされない。二重なチェックは不要だが、製剤製造所は、原薬製造所に関する情報を製造販売業者からしっかりと入手することが必要で、不足があれば、直接、監査することも必要となる。また、原薬製造所への監査において、原薬製造所が行う原料等の製造施設との取り決めや監査結果を確認することも必要である。原料が起因する異物や汚染を確認するには、現場の確認が必須である。直接の容器が原因で、安定性に影響することもある。吸湿性や遮光性も考慮することは当然だが、原薬や製剤バルクとして、保管する際に利用するポリ袋など、容器からの可塑剤等が滲出することもリスクとして考えるべきである。資材の組成は、社外秘で、開示されないことも多い。監査で確認すべきことは、製剤等の品質に影響する可能性の事象について、いかにして、確認するかである。当局の査察とは別の見方をしなければならない。
パッケージメーカーへの監査で、紙粉が多いと指摘しても無駄である。それより、大切なことは、印刷内容が適切に管理されていることや印刷に誤植やカスレなどがなく、適切に印刷されていることにある。この取り扱いもデータインテグリティの確保である。版の管理や印刷物のチェック方法も監査で見るべきポイントとなる。品質情報等を年次レビューして、リスク分析をしたうえで、監査を行うことが必要である。製造物により、監査の確認すべきポイントが変わるのは当然である。その点を踏まえて監査を行わないと、意味のない監査となってしまう。監査員は、その点を十分認識し、その製造する製品の品質を把握し、その工程での重要な点を理解し、最終製品へ与えるリスクが、その原料、資材の品質のどの点にあるかを考えて、監査をしなければならない。その場しのぎの重箱の隅をつつくような誤字脱字の指摘をしてはならない。
2ページ中 1ページ目
コメント
/
/
/
この記事へのコメントはありません。
コメント