固形製剤のスケールアップ【第7回(最終回)】
2014/02/24
製剤
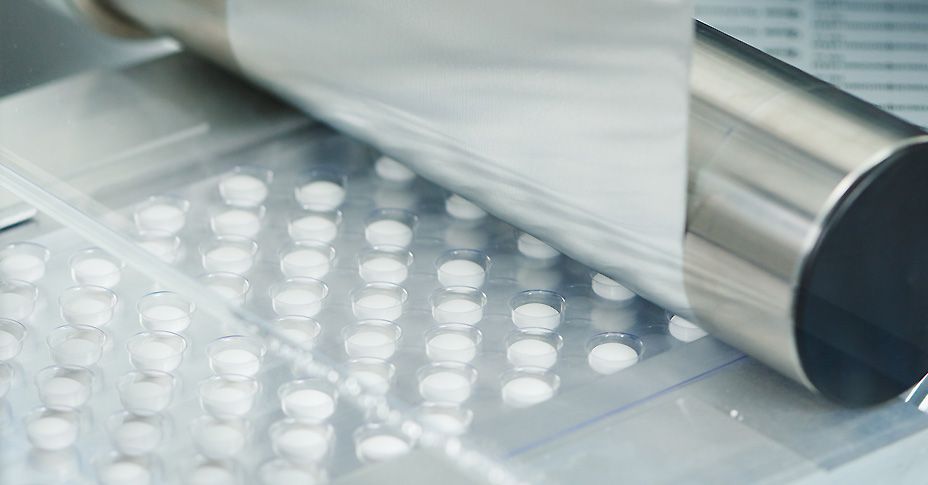
はじめに
これまで6回にわたって固形製剤のスケールアップについて話を進めてきたが、今回が最終回ということで、連続生産方式におけるスケールアップについて述べてみたい。
バッチ生産とは違って、連続生産はもともとスケールアップが必要のない生産システムとして現在非常に注目されている。バッチ生産で行われている単位操作も、極小バッチを連続的に処理する疑似連続生産方式が検討され、そのいくつかがすでに商品化され、紹介されているほどである。
固形製剤の連続生産方式としては、粉砕、打錠、カプセル充填、錠剤印刷、検査、包装などがその例であるが、ここではまず連続生産方式のメリットと課題を取り上げ、続いて連続生産方式のうち、打錠について取り上げ、そのスケールアップについて考察する。
1.連続生産方式のメリットと課題
固形製剤における生産プロセスでは、それぞれの単位操作で連続生産とバッチ生産が入り混じっていることが多い。例えば、固形製剤の代表的剤形であるフィルムコート錠の場合、まず連続生産方式により原料の粉砕や篩別が行われる。続いてバッチ生産方式により造粒が行われる。もっとも、造粒であっても乾式造粒の場合は連続生産である。続いて、連続生産による整粒が行われ、さらにバッチ生産による混合へと続く。次に連続生産による打錠で錠剤がつくられ、バッチ生産によるフィルムコーティングが施される。さらには連続生産による検査が行われて、同じく連続生産による包装が行われ、最終製品として出荷される。このように、固形製剤のプロセスは連続生産方式とバッチ生産方式とが組み合わされて全体を構成している。できればバッチ生産のみ、あるいは連続生産のみで構成されていれば、全体の効率がよくなることは想像に難くない。
連続生産の強みは、何と言ってもスケールアップが必要ない、あるいはやさしいことにある。多くの場合、パイロットスケールの生産設備はそのまま生産スケールの設備になり得る。したがって、研究所で検討した内容をそのまま生産現場で生かすことができ、技術移転も容易になり、非常にメリットが大きい。また、昨今新たな問題になりつつあるデザインスペースのスケールの違いによる検証も必要なくなる*1。また、連続生産方式のもう一つのメリットは、ロットサイズをいかようにも調整できることにある。生産要請量は時として大きく変動する。その時、大きくなる場合はバッチ生産でも数をこなせばよいので、まだ対応できるが、小さくなる場合はバッチ生産では対応が難しく、過剰在庫を抱えることになる。ところが、連続生産の場合は必要量だけ生産することができるので、非常にフレキシビリティが高い。取分け製薬産業のような少量多品種生産の場合には、このメリットは大きい。
一方で問題点もある。医薬品のような非常にセンシティブな製品では、ロット内の均一性が非常に重要な品質特性となる。連続生産においては、生産中ずっと製品が均一であることをどのように保証するかは、非常に難しい課題である。生産中に頻繁に、理想的には連続的にモニタリングをして、常に同じ品質の製品ができていることを保証することが望ましいが、実際にはこれはかなり難しい。最近になってPATツールの開発が進展し、以前に比べればかなりモニタリング技術は整いつつあるが、それでも均一性を保証することは容易ではなく、また投資も必要になる。
これらのメリットや課題を考慮しつつ、どのような生産方式を選択するかは、現在選択し得る生産技術と企業側のポリシーに依存している。
-----------------------------------------
*1:ICH Q8ガイドラインには「デザインスペース内で運用する(条件を変動させる)ことは変更とみなされない」と書かれているが、最近FDAは実生産スケールで確立したデザインスペースでない限り、条件を変えれば変更に相当すると言い出している。
-----------------------------------------
5ページ中 1ページ目
コメント
/
/
/
この記事へのコメントはありません。
コメント