GMPヒューマンエラー防止のための文書管理【第53回】
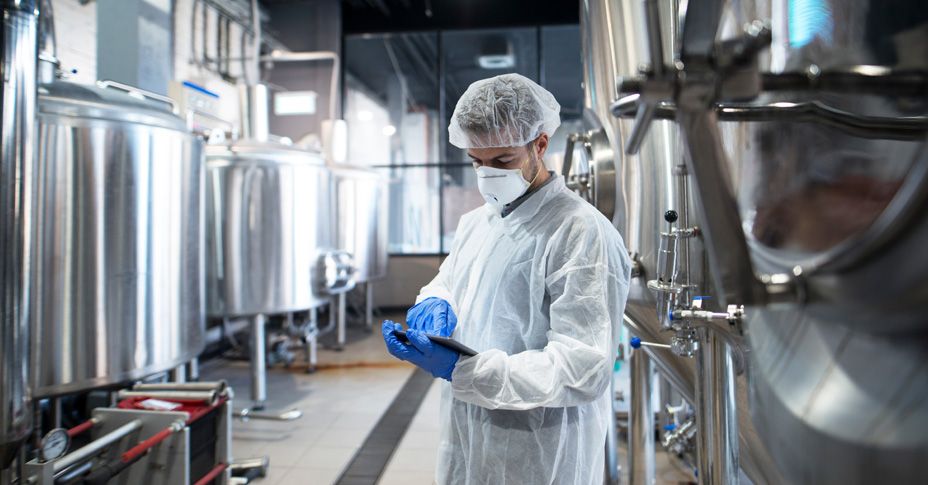
今回もQA活動について引き続き解説する。
QA活動
1.使わないSOP
ヒューマンエラー発生時に、教育訓練不足を嘆く施設は多い。特に、SOPからの逸脱の場合、教育訓練不足を原因として問題解決させることは多い。しかし、ヒューマンエラーを起こした作業者によると、以前から行っていたとか、そのように指導を受けていたなどと聞くこともある。手順書を確認していなかったとか、手順書を十分理解できなかったとかの話にはなるが、本当にそのSOPは必要だったのだろうか。SOPに従い、指図通りに作業を行うことは、GMPの基本である。しかし、作業の都度、SOPを読まなければならないような作業者が行う工程に心配はないのだろうか。ベテランになればなるほど、そのプロセスを熟知しているだろう。その都度、SOPを読んでいたら、作業が非効率になってしまい、安定供給なんてままならないのではないだろうか。都度都度、SOPを読まないと作業ができない新人にその作業を任せるのは不安である。GMPがSOPを要求するのは、「誰でもその作業が行えるため」と説明する方もいるが、私はその考えは間違いだと思う。SOPは、そのプロセスを確立するためであり、そのプロセスに間違いがないよう検証されていることを示すものである。当然、その作業するにあたり、教育訓練を受け、適切に作業を行えるかどうか判定されなければならない。その判定を受けたものが、いちいち、SOPを見ながらしか、作業ができないなら、その作業者は、その作業を理解していないと思われる。熟知した作業者でもミスをすることはある。他の品目と困惑して間違えやすい点を指図書に明記し、作業者は指図書のみ確認すればよい状況を作らなければならない。その上で、新人への教育プログラムとなる手順書等を整備し、教育訓練そのものを新人、一人で作業ができる者、教育指導ができるベテラン等レベル評価を行わなければ、実効性のある教育訓練は成り立たない。また、SOPや指図の位置づけも明確にし、効率的な作業を行える体制が必要である。
製造手順などのSOPを製品標準書ごとに作成している製造所は多い。しかし、そのSOPの利用度を聞くと、あまり利用されない状況である場合がある。ヒューマンエラーが起きたとき、SOPを確認しなかったからと原因分析されているケースで、その作業ごとにSOPを確認していたかを聞くと、そもそも、そのSOPはあまり利用せれていなかったことが判明することが多い。なぜ、そのSOPが利用されていなかったかを尋ねると、その作業自体を作業者が熟知しており、その都度、読まなくても作業を行うことができたのである。では、なぜそのエラーが起きたかというと、他の品目と勘違いなどによることが多い。同じ製造ラインや製造装置で、何品目も製造されることが多い中、その工程での工程管理値などの設定値やパラメータなど、品目により異なる点を示すことが重要であり、個々の品目の製造手順書にすべての操作方法を同じように記載する必要はない。かえって、同じ内容を多くの文書に記載することで、エラーを引き起こすことになる。製造ラインや装置の操作手順書をラインや装置ごとに作成して、個々の品目の製造手順書には、そのラインや装置での工程管理値としての設定値やパラメータを記載するべきである。その方が作業者にとっても、品目により製造手順の異なる点が明確になり、エラーを起こすことを減少させることになる。
ヒューマンエラーを減らすためには、まず、使うSOPを持つことにある。文書の整理をする時、使わないSOPを整理することより、SOPを使いやすくすることを優先しなければならない。そして、重要なことは同じことを二つの文書に書かないことである。
2ページ中 1ページ目
コメント
/
/
/
この記事へのコメントはありません。
コメント