GMPヒューマンエラー防止のための文書管理【第40回】
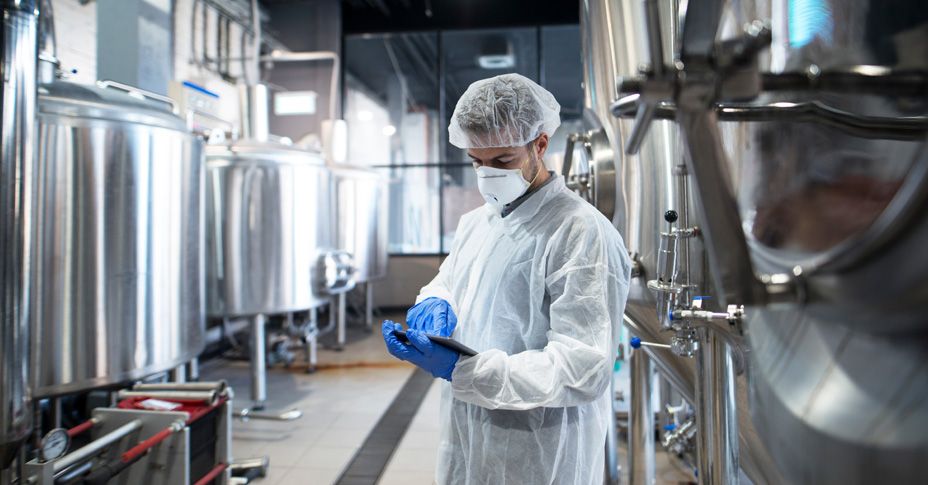
1.何故、取り違えは起こったか
小林化工の「イトラコナゾール錠50『MEEK』」に「リルマザホン塩酸塩水和物」が混入し、回収に至った。この事例は、作業者だけでなく、いくつものヒューマンエラーが重なり発生した。この事例を解析しよう。読売新聞1)によると、
1錠あたり5㎎の睡眠導入剤成分が混入していた。通常の最大投与量の2.5 倍。1日8錠服用する人もあり、その場合は20 倍に相当する。
何故、イトラコナゾール錠50製造中の現場にリルマザホンがあったのか。製造中の製造室に、他の製品を保管することは交差汚染防止及び混同防止の観点から認められない。製造過程の目減り分の原薬を補充すること自体、含量均一性などの点から検証されているか疑問点はあるが、今回は、ヒューマンエラー防止の観点から考える。今回の事例のようなことが起きないようラインクリアランスを徹底し、製造中の製造室には、他の品目の原料等を持ち込むことはできない。どこで、取り違いが起きたのかを考える。原薬、原料は、原料倉庫で保管されており、表示ラベルやエリアを指定し、保管管理されている。受入試験合格後に、指図等により製造現場に払い出される。次に製造現場に持ち込まれる。指図に基づく原料等が払い出されたかを確認する。ここで取り違い防止の確認として①倉庫からの払い出しの確認②製造現場での受け入れの確認の2点がある。
製造エリア内に、倉庫から払い出された品目や製造での施用残を保管する場合もある。保管にあたり、交差汚染防止や混同防止の観点から保管容器や表示ラベル等により、識別が容易にできるよう保管されている。施設によっては、MES(生産管理システム)を利用し、混同防止対策を行っている。今回の事例では、MES等のシステムを利用していないようである。しかし、例えシステムを利用していたからと言って、完全に防げるわけではない。識別用のバーコードラベルの貼付の間違いやバーコードリーダーによる読み取りをまとめて行ったりすることで、払い出し品を取り違いする可能性はある。いかにシステムを利用しても、作業者がミスに対してリスクを認識しなければ、逸脱は発生する。
製造開始は、まず、秤量工程である。製造エリア内の一時保管場所から秤量室への持ち出しは、誰が行うのか。秤量担当者1人であると、ダブルチェックができない。MESの利用と人による確認でのダブルチェックも可能であるが、その際にシステムを信じるあまり、人の確認不足が起こる可能性は高い。秤量がその品目で使用する原料をまとめてすることもあろう。共通原料等の秤量では、交差汚染防止に努めなければならない。今回の事例では、他の品目である睡眠導入剤が秤量室にあったことでの取り違いである。混同防止の観点からあってはならないことである。今回、目減り分の補充としての追加投入である。その秤量が造粒室等の秤量室以外の製造室で行われた可能性がある。原薬の追加投入すること自体が製造販売承認書に記載がないことは問題であるが、その作業についての手順書もあり、2人で行うことやダブルチェックをすることも規定されていたようである。手順書に沿って、2人の作業者で作業できなかったことが問題であったが、そのことを現場の責任だけでなく、会社として、そのようなことを行っていたことを認識していなかったこと自体が問題である。
2ページ中 1ページ目
コメント
/
/
/
この記事へのコメントはありません。
コメント