リスクアセスメント&マネジメント(RAMP)【第8回】
2015/09/03
品質システム
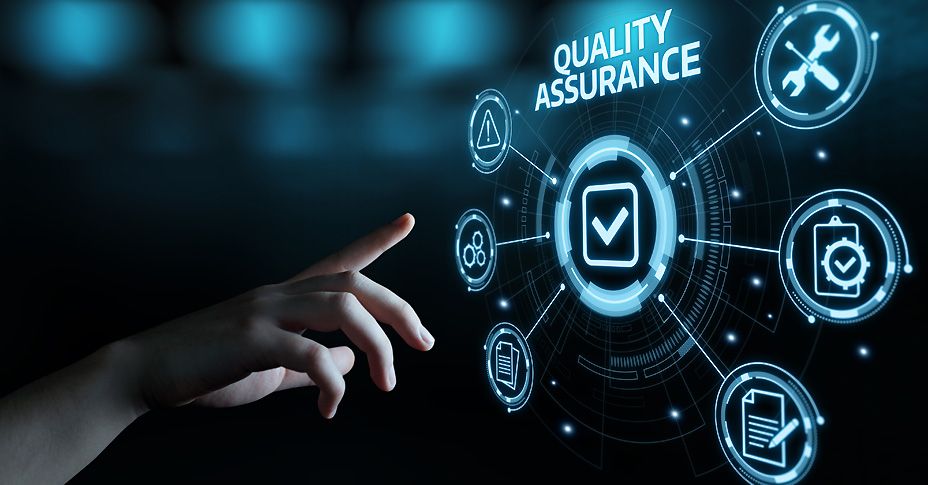
"(4.リスクベースバリデーションに関し、前回の続き)
4-2 プロセスバリデーション
現在、FDAはプロセスバリデーションの要求連続成功バッチ数は明記していない。FDA の意図では、プロセスに潜在するリスクを評価・軽減するに必要なバッチをバリデーションすることを要求している。またパラメーターの限度値を上下に逸脱した条件が品質にどのように影響するか、つまりは、パラメーターの逸脱のリスクを評価すること、もしくは品質に影響を与えないパラメーターの範囲をバリデーションすることで、リスクを軽減することになる。結果、これらの条件を検証することには、連続3バッチでは充分な数でないことをFDAは示唆している。
要約すると、プロセスバリデーションとは:
製造におけるリスク評価とは、製品が、計画された安全性、有効性、安定性及び性能を保持していることを担保するため、予め定められた範囲内で管理されることが必須である工程、それにより定められる品質特性を評価することとなる。逆説的には、患者に対して影響を及ぼす品質を損なう工程、もしくは予め定められた範囲外で製造して品質を損なう範囲を評価することも含むことになる。
機器の適格性確認と同様に、製造に用いる変動範囲(管理幅)が評価され、worst case(規格外;OOS)を防ぐために、製造パラメーター、工程内試験に対するalert/action levelの設定が可能となる。
このアラート・アクションレベルの設定の有無、設定されているならば、その設定根拠・見直しの頻度が監査項目となる。さらに年次照査において、アラート・アクションレベルの妥当性の確認・検証、その検証結果に基づきアラート・アクションレベルの見直しの必要性の確認等も監査項目となる。
別の言葉を借りれば、製品の品質の恒常化にアラート・アクションレベルが、判断手段として用いられるからである。また、アラート・アクションレベルに達したとき、どのようにCAPAを行って、品質の保全に役立てたかが、リスクマネジメントに繋がる。
4-3 再バリデーション
再バリデーションは、言葉を変えればリスクの再評価といえる。それは、技術の進歩、機械・機器の経年劣化、環境の変化で、リスクの大きさ・質が、最初のバリデーション・リスク評価時と異なってくることは、自明である。リスクの再評価は、ここにリスク評価を行うことに代えて、年次照査を行うことでも可能である。年次に、品質等を見直すことで、リスクを評価は可能ですが、大きな変更があれば、再度バリデーション・リスク評価が必須となる。
"
4-2 プロセスバリデーション
規定された工程(規定された成分を含む)を用い、最終製品の一連のバッチが通常の条件下で製造される。理論的には、工程の繰り返し回数及び観察された内容により、通常の変動の程度及び傾向がわかり、また評価の為の十分なデータが提供されなければならない。最終的に合意したパラメーター内での連続3バッチ/操業が、プロセスバリデーションを成立させることについては、一般的に受け入れられている。
現在、FDAはプロセスバリデーションの要求連続成功バッチ数は明記していない。FDA の意図では、プロセスに潜在するリスクを評価・軽減するに必要なバッチをバリデーションすることを要求している。またパラメーターの限度値を上下に逸脱した条件が品質にどのように影響するか、つまりは、パラメーターの逸脱のリスクを評価すること、もしくは品質に影響を与えないパラメーターの範囲をバリデーションすることで、リスクを軽減することになる。結果、これらの条件を検証することには、連続3バッチでは充分な数でないことをFDAは示唆している。
要約すると、プロセスバリデーションとは:
製造におけるリスク評価とは、製品が、計画された安全性、有効性、安定性及び性能を保持していることを担保するため、予め定められた範囲内で管理されることが必須である工程、それにより定められる品質特性を評価することとなる。逆説的には、患者に対して影響を及ぼす品質を損なう工程、もしくは予め定められた範囲外で製造して品質を損なう範囲を評価することも含むことになる。
機器の適格性確認と同様に、製造に用いる変動範囲(管理幅)が評価され、worst case(規格外;OOS)を防ぐために、製造パラメーター、工程内試験に対するalert/action levelの設定が可能となる。
このアラート・アクションレベルの設定の有無、設定されているならば、その設定根拠・見直しの頻度が監査項目となる。さらに年次照査において、アラート・アクションレベルの妥当性の確認・検証、その検証結果に基づきアラート・アクションレベルの見直しの必要性の確認等も監査項目となる。
別の言葉を借りれば、製品の品質の恒常化にアラート・アクションレベルが、判断手段として用いられるからである。また、アラート・アクションレベルに達したとき、どのようにCAPAを行って、品質の保全に役立てたかが、リスクマネジメントに繋がる。
4-3 再バリデーション
洗浄を含めた、施設、システム、装置及び工程は、それらが有効であることを確認する為、定期的に評価することがリスク管理では、求められている。バリデーション済の状態に対し重大な変更が行われていない場合には、施設、システム、装置及び工程が所定の要件に適合するという証拠を伴うレビューを実施することで、再バリデーションとみなすことが出来る。
再バリデーションは、言葉を変えればリスクの再評価といえる。それは、技術の進歩、機械・機器の経年劣化、環境の変化で、リスクの大きさ・質が、最初のバリデーション・リスク評価時と異なってくることは、自明である。リスクの再評価は、ここにリスク評価を行うことに代えて、年次照査を行うことでも可能である。年次に、品質等を見直すことで、リスクを評価は可能ですが、大きな変更があれば、再度バリデーション・リスク評価が必須となる。
"
2ページ中 1ページ目
コメント
/
/
/
この記事へのコメントはありません。
コメント