医薬品委受託製造に関する四方山話【第10回】
2014/06/30
製剤
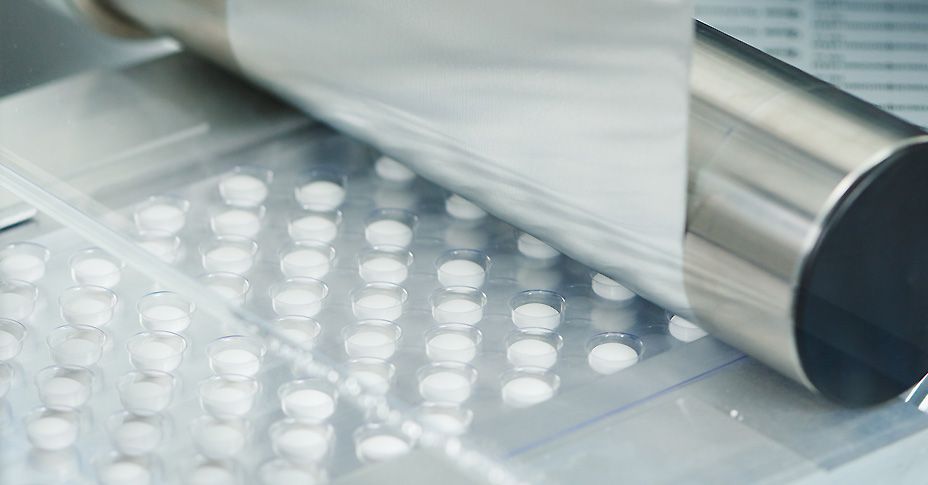
22.筆者の実務体験(原薬)
筆者は前職の原薬製造法開発部門時代に、Process Chemistとして、社内における技術移転を数度経験していますので、その時の経験から少しお話を進めたいとおもいます。今から20年ほど前のことですので、今のアカデミックな研究者に通じるかどうかという懸念はありますが、少しでも考え方の参考になればとおもいます。まず、対象はPhase 1原薬を初めてGMP施設で製造する場合をイメージしてください。私の経験では、この場合担当するProcess Chemistは自らが主体となって、少なくとも2度社内技術移転を実施します。まずは、1)自らが移転元に出向いて技術移転を受けるMedicinal ChemistからProcess Chemistへの技術移転、2)Process Chemistによるプロセスの改良(合成ルート変更やスケールアップを含む)、そして、3)パイロットプラントでの現場製造実施者への技術移転です。最初に、創薬研究部門で動物試験用として設定されたNon-GMPの合成ルート、合成法の開示、説明を受けます。化学者であれば、化学構造式で示された合成ルートと反応条件、後処理方法、収率等の情報さえ見れば、大凡どの工程のスケールアップが難しく、既存の設備で実施可能かどうかなどが掴めます。しかし、実際に文書で見るのと現場を見るのは大違いですので、まずはそのルートで合成された原薬の物性、品質をしっかり頭に置いた上で、合成担当者にどこの工程、プロセスが勘所になるのか直接聞き取り調査をし、例えば1kg-2kgのラボでの合成実験を直接観察することが早道だとおもいます。また、その合成ルートが既存特許を侵害していないか等の調査も非常に重要です。キロラボでは可能であった製造が、スケールアップしたGMP施設では適用できない例は枚挙にいとまがなく、必ずといっていいほどこの時点で大きな変更が発生します。最近では、重要なGLP試験に使用される原薬の品質から商用原薬の品質一貫性を問われるようになり、キロラボスケールにProcess Chemistが入り込み開発初期(前臨床)からの技術移転が行われるようになってきています。そのため、CMCのProcess Chemistは、どこの新薬メーカーでも引っ張りだこになっているのではないでしょうか?開発の上流から携わり、自らスケールアッププロセスを見出し、製造現場に技術移転をし、モノづくりを完成させ会社に大きな貢献する、そのような仕事に遣り甲斐を感じるProcess Chemistがもっと増えると日本のモノづくりはもっと活性化するのではとおもいます。余談が長くなりましたが、キロラボでの合成実験ノートを見せていただき、ポイントを学び、自らトレース実験をし、既存設備で実施可能かどうかを判断するのが次の仕事です。開発初期は、スピードがとても重要であることは明白ですので、できる限りそのままスケールアップできることを願うのですが、通常はそうはいきません。反応の種類によっては、冷却速度が追いつかず暴走系になって爆発する危険があったり、作業者が扱えないような人体への作用がある中間体を経由する場合、高温/超低温の反応があったり、微細な結晶で固液分離ができないなど、様々な課題が抽出されてきます。それらを改良してスケールアップ処方を確立することがProcess Chemistryの醍醐味で、その次が、それを実際の製造現場で実現することになります。私も、当時、そのような仕事が楽しくて自ら進んでAnalytical ChemistからProcess Chemistへの道に進んだのですが、最初は失敗続きで技術移転というよりは、現場で製造している人たちから教えられる毎日でした。フラスコで観察されている事象を反応釜でどう実現するか、現場の方々と一緒に実験室でコルベンを並べて夜遅くまで議論し、プロセス構築した日々を懐かしく思い出します。実は、私が最初に担当した原薬中間体工程の製造1ロット目は大失敗でした。反応液の低温冷却操作(-55℃)に失敗して固化し、再溶解中の分解でなんと標準収率の半分程度になってしまったのです。冷却しすぎると固化することを文書化し伝えていなかったこと、パイロットスケールでの反応釜のジャケット中の冷媒の冷却操作でそのようなことになる危険性を理解していなかったことがそもそもの原因でした。しかし、私の担当上司の見る目があったのでしょうか、その1ロット目のみ1/5スケールで実施しており、その後、2ロット目実施までに夜を徹してプロセス改良を行い、次の4ロットフルスケール生産で必要量を賄えたことは今でも嬉しい新鮮な記憶として残っています。この時のプロセス構築の実験と技術移転、現場の方々との議論は、大きな失敗をしたこともあり、製造法の技術移転をしっかりやることの重要性を現場レベルで知った最初でした。この時に、もうひとつ学んだのは、現場を知ること、実際にオペレーションする人の意見をしっかり聞くことです。どこが問題になるかを自ら考え意見交換し、場合によれば標準を変更することです。既成概念に捉われず、自分の作った標準に過信は禁物と実体験で学んだことは、以後の財産になりました。実は、私の原薬製造における技術移転の経験では、その後もいくつか失敗しているのですが、長くなりますので次は固形剤の技術移転に移りたいとおもいます。
4ページ中 1ページ目
コメント
/
/
/
この記事へのコメントはありません。
コメント