ソー責のソー肩にはソー当重い責任がのっている!【第8回】
2014/06/30
製剤
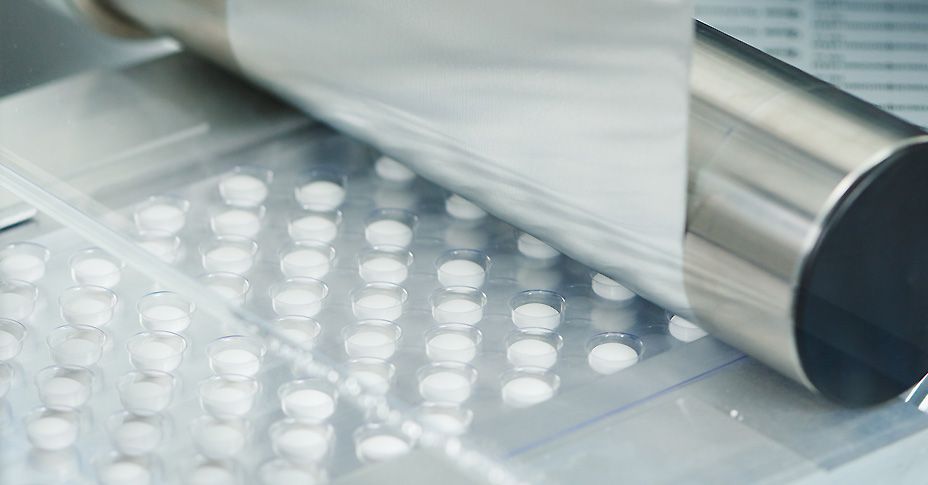
はじめての製剤工場
2001年4月に岐阜工場から小田原工場へ異動、前任の品質管理部長が体調を壊したため急遽製剤工場の品質管理を経験することになった。小田原工場は、赴任する4ヶ月ほど前に自主回収を行っていたことから、工場の雰囲気は決して良いものではなかった。
赴任して直ぐに原薬工場と製剤工場は違いがあると感じたのはクレーム処理であった。そして、赴任して一か月後、そのクレームの洗礼を受けた。
1.クレームの洗礼
まず、製剤工場と原薬工場の違いは、苦情にあることが分かった。5月に、医師がアンプルをカットするときに怪我をしたという苦情が、初めて受けたクレームであった。
どうして怪我をするのかということから、チャレンジ試験、調査を進めた。アンプルがどのようにして割れるのか、どの位の力で割れるか、実際に品質管理のメンバーに製品数百本をカットしてもらい、通常の方法で怪我をすることがあるかなども調べた。また、他社の同様製品との比較なども行う。結果、アンプルに問題は無いという結論に達し、医療機関にアンプルのサンプルも持参し、正しいカットの仕方について説明し、実際に試験してもらい製品に問題が無いことを理解して頂くことができた。これが製剤工場異動後、はじめての苦情処理であった。このクレームから医療現場では、思いもよらぬ方法でアンプルのカットが行われていることも知った。
その次に受けたのが、「バイアルに虫が入っていた」と言うクレームである。虫の混入は確実に回収につながる。クレーム現品は、バイアルにガラス注射筒に針が装着され、バイアルに刺さったままの状態で送られてきた。観察すると注射筒側に虫が入っている。慎重に取り扱い顕微鏡で観察するとその虫の形状は脚も翅もすべて揃っている完全な虫体であった。
届いた当日、すぐに技術室の若手が工場周辺で網をもって昆虫採集を実施、似たような形の虫を集めてきた。その採取してきた虫をバイアルの中に入れ、送られてきた注射針と同じサイズの18Gの針を用いて吸入するというチャレンジ試験を行った。注射筒に吸入した時に虫が変化するかを調べるためである。その結果、何度やっても針を通るときに虫は破壊され、翅や脚が外れることが分かった。そのことから、バイアル内に入っていたのであれば、虫が破壊される。クレーム現品の注射筒側にあり、完全体であったので、針を通して吸い込まれたのであるはずがない。そのことから虫はバイアルにあったのではないと判断できた。その他、多くの調査を進めた。徹夜で考察を報告書にとりまとめた。ちなみに、同定した結果、当該の虫はクロバネキノコバエであった。その報告に医療機関を訪問、了解を得ることができた。現物を観察し、科学的に考え、そして工場が総力をあげ、問題を解決することが、いかに大切かを認識させられた。苦情については、製剤工場、本社総括製造販売責任者の10数年にわたり、経験を積むことになったが、虫のクレームの解決が、製剤工場での色々な課題解決の原点でもある。そして、現物、現場、現状をみるという三現主義は製剤工場でも基本であることを再認識した。
そのようにして苦情の洗礼を受けたが、製造現場で中々解決しない問題があった。それは、設備は設置したものの、どうしてもゴム栓の異物が洗浄できないため半年も稼働ができない新型のゴム栓洗浄機である。面子を捨てて、先行して同じ装置を導入し、稼働しているT社のS工場に教えを請おうと技術者をつれてS工場を訪問した。そこで分かったのは、ゴム栓は水滴がつくと乾燥する間にゴム栓の中から褐色の異物が表面に浮かび上がってくるということであった。このような情報は、機械メーカーからは何も得られなかった。T社の長年の経験、ナレッジは素晴らしく、その会社の力を再認識することとなった。そしてそれを教示して頂いたことに深く感謝するものである。異動して間もない頃のことで忘れられない。
5ページ中 1ページ目
コメント
/
/
/
この記事へのコメントはありません。
コメント