連続生産【第1回】
2018/02/23
製剤
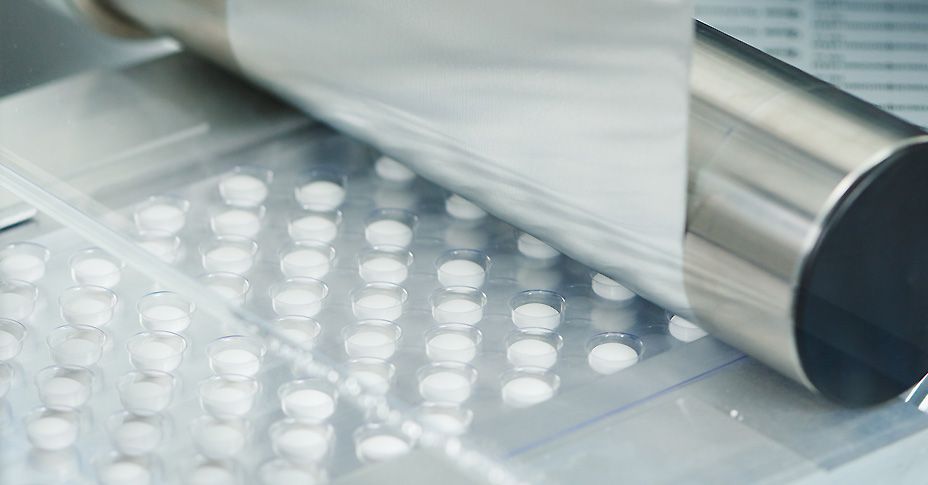
はじめに
連続生産は、食品や石油化学製品等の製造では既に導入されている生産方法である。医薬品製造においてはバッチ生産が一般的で、連続生産の導入は遅れていたが、2015年に嚢胞性線維症治療薬Orkambiが連続生産を導入した初めてのケースとして米国FDAにより承認された。また2016年には同じく米国FDAより、既に承認されているHIV感染症治療薬Prezistaのバッチ製造から連続生産への変更が承認された。日本では現時点では承認例はないが、近い将来承認品目が出ると思われ、現在注目されているトピックの一つである。そこで本シリーズにおいて連続生産について取り上げる。
1. 連続生産の概要
従来のバッチ生産は、原材料を製造工程内に投入後、生産物を一度に取り出す生産方法で、ある操作単位の内容物と他の単位の内容物との交差は製造中には起きない。一方、連続生産は原材料を連続的に製造工程内に投入し、生産物を連続的に取り出す生産方法とされている1)。しかし、まだ国際的なガイドラインがなく、万国共通の正規の定義は存在していない。現在ICH(医薬品規制調和国際会議)において連続生産を取り上げることも検討されているが、ガイドライン化はしばらく先と思われる。連続生産と言っても現状においては様々なケースが想定され、その示す範囲は幅広い。図1に示す通り、原材料投入から最終生産物を取り出すまでのすべての工程を1台の機器で製造を連続化することが純粋な連続生産と言えるが、医薬品製造においては現状では各工程の機器は独立しており、その間は輸送管で結ばれ重力若しくは空気の流れに乗って各工程の生産物が移動していくのが一般的である。そしてすべての工程が連続化されていることは稀で、工程の一部のみを連続化し、連続化できない工程においては複数機を時間差で常に1台以上を運転することによって連続的に生産物を排出する仕組みを取っている。各々の製造工程を見てみると、現状では混合や造粒、乾燥、打錠工程は既に連続化が可能となっているが、錠剤コーティングは完全な連続化はまだ技術的には追いついていない。工程を一部のみしか連続化できない、若しくはしていない理由としては技術的な要因もさることながら、コスト的な要因も含まれていると思われる。
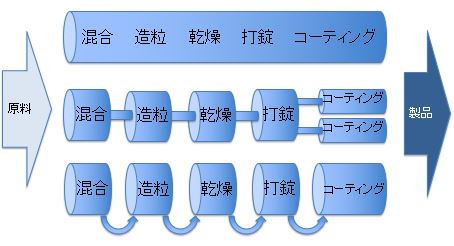
図1 連続生産の理想(上)と現実(中)、バッチ生産(下)の模式図
2. 連続生産のメリットとデメリット
バッチ生産と比較した連続生産における利点としてしばしば取り上げられている点として、稼働時間により生産量のコントロールが可能であり、製剤開発時にスケールアップ検討が基本的に不要となること、需要に応じ生産量の増減が可能となり、製造・保管コストの削減が期待できることが挙げられる。また、大規模な設備が不要となることから省スペース化が実現できること、そして製造サイトの設置・移動も容易になる。実際には海外ではプラントをトラックで輸送して、1週間ほどで組み立てるというようなことも行われているようである。工程が連続化・一体化することにより人が関わる作業も減ることから、作業員の安全性向上に繫がり、人的エラーやコストを減らすことができる。一方、欠点としては現時点ではこれまでの経験、知識の蓄積が十分にないことから開発、運用が難しいこと、承認申請、GMP上の取り扱いを含め規制上の取り扱いについて明確化されていない点が多いことが挙げられる。
連続生産は、食品や石油化学製品等の製造では既に導入されている生産方法である。医薬品製造においてはバッチ生産が一般的で、連続生産の導入は遅れていたが、2015年に嚢胞性線維症治療薬Orkambiが連続生産を導入した初めてのケースとして米国FDAにより承認された。また2016年には同じく米国FDAより、既に承認されているHIV感染症治療薬Prezistaのバッチ製造から連続生産への変更が承認された。日本では現時点では承認例はないが、近い将来承認品目が出ると思われ、現在注目されているトピックの一つである。そこで本シリーズにおいて連続生産について取り上げる。
1. 連続生産の概要
従来のバッチ生産は、原材料を製造工程内に投入後、生産物を一度に取り出す生産方法で、ある操作単位の内容物と他の単位の内容物との交差は製造中には起きない。一方、連続生産は原材料を連続的に製造工程内に投入し、生産物を連続的に取り出す生産方法とされている1)。しかし、まだ国際的なガイドラインがなく、万国共通の正規の定義は存在していない。現在ICH(医薬品規制調和国際会議)において連続生産を取り上げることも検討されているが、ガイドライン化はしばらく先と思われる。連続生産と言っても現状においては様々なケースが想定され、その示す範囲は幅広い。図1に示す通り、原材料投入から最終生産物を取り出すまでのすべての工程を1台の機器で製造を連続化することが純粋な連続生産と言えるが、医薬品製造においては現状では各工程の機器は独立しており、その間は輸送管で結ばれ重力若しくは空気の流れに乗って各工程の生産物が移動していくのが一般的である。そしてすべての工程が連続化されていることは稀で、工程の一部のみを連続化し、連続化できない工程においては複数機を時間差で常に1台以上を運転することによって連続的に生産物を排出する仕組みを取っている。各々の製造工程を見てみると、現状では混合や造粒、乾燥、打錠工程は既に連続化が可能となっているが、錠剤コーティングは完全な連続化はまだ技術的には追いついていない。工程を一部のみしか連続化できない、若しくはしていない理由としては技術的な要因もさることながら、コスト的な要因も含まれていると思われる。
図1 連続生産の理想(上)と現実(中)、バッチ生産(下)の模式図
2. 連続生産のメリットとデメリット
バッチ生産と比較した連続生産における利点としてしばしば取り上げられている点として、稼働時間により生産量のコントロールが可能であり、製剤開発時にスケールアップ検討が基本的に不要となること、需要に応じ生産量の増減が可能となり、製造・保管コストの削減が期待できることが挙げられる。また、大規模な設備が不要となることから省スペース化が実現できること、そして製造サイトの設置・移動も容易になる。実際には海外ではプラントをトラックで輸送して、1週間ほどで組み立てるというようなことも行われているようである。工程が連続化・一体化することにより人が関わる作業も減ることから、作業員の安全性向上に繫がり、人的エラーやコストを減らすことができる。一方、欠点としては現時点ではこれまでの経験、知識の蓄積が十分にないことから開発、運用が難しいこと、承認申請、GMP上の取り扱いを含め規制上の取り扱いについて明確化されていない点が多いことが挙げられる。
2ページ中 1ページ目
コメント
/
/
/
この記事へのコメントはありません。
コメント