GMPヒューマンエラー防止のための文書管理【第10回】
2018/06/01
品質システム
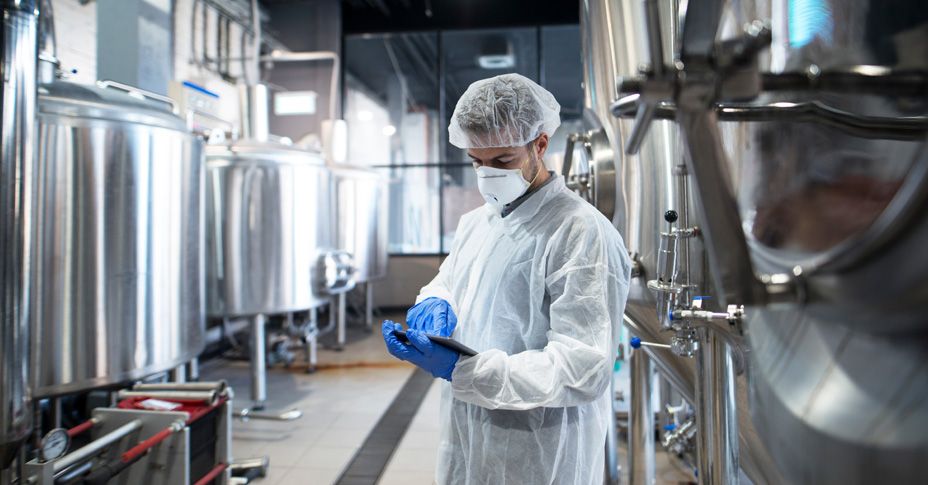
1. 断捨離
「断捨離(だんしゃり)とは、不要な物を減らし、生活に調和をもたらそうとする思想」1) とある。査察等の際、医薬品製造所の製造室に使用しなくなった設備があると、異物混入や交差汚染の原因となるため、撤去するよう指導される。原材料や資材の場合は、混同防止の観点から、撤去するよう求められる。では、文書の場合はどうだろうか。使用していない文書等の改訂や廃止を行うことは必要である。しかし、廃止した品目のSOPや使用禁止となった設備の操作手順が残っていることはあるだろう。手順書の内容すべてが廃止になることも少ない。倉庫管理手順に保管する品目名を記載していることも多い。しかし、その品目一覧に扱わなくなった品目名の記載が残っていたり、追加しなくてはならない品目名の記載がなかったりすることもある。手順書ごとに対象品目を記載する必要はない。いろいろな手順書とトレースができる品目一覧を別途作成すればよい。製品標準書にその品目で使用するSOPをきちんと記載し、トレースが取れるようにすれば済む問題である。しかし、今までの管理だからと、文書管理の改善が進まない製造所も多い。文書の整理も、断捨離として、ある段階で踏ん切りをつけないと思うように進まない。過去の文書管理と決別することも必要である。
ルールは、その時の状況等で変更されなければならない。ある作業が手順書の記載内容と齟齬があると、逸脱処理するケースは多いと思う。その逸脱は、医薬品の品質に関わるのだろうか、リスク分析が必要である。しかし、文書の改訂を必ず変更管理をする必要はない。変更管理の対象でなければ、リスク分析を行わないことになる。手順書の改訂が、その製造方法や試験方法、管理方法にならないなら、リスク分析は不要である。手順書や記録用紙などの断捨離は、難しいものである。製造や試験の現場の実態と合わせる必要がある。チェックシートなどが現場の負担となっていることも多い。本来、その場で確認すべきチェックを作業終了後のチェックになっている可能性もある。チェックは、現場で必ず確認しなくても、チェック機能が有効なものでなければならない。例えば、清掃記録で、清掃状態を直接、確認せずにチェックする場合、その清掃作業者の普段の清掃方法等を把握しているなら、清掃の作業者をチェックすることで、清掃状況の確認をしたともいえる。その場合、清掃作業のスキルを明確にした教育訓練等の記録がその根拠となる。現場でのチェックをする場合、清掃作業が2人で行うなら、相互に記録者と確認者として、清掃状態の確認をし、記録する方法もある。工程責任者が必ずチェックするのではなく、権限を委譲し、ラインリーダーが現場確認するなど、チェックが有効なものとなるようしなければならない。チェックが必要かどうかも検討し、品質へのリスクがあるかチェック項目を検討してほしい。チェックが形がい化しないようチェックを増やすのではなく、重要なチェックをきちんとチェックした記録としなければならない。無駄で不要なチェックを削減することで、チェックが有効なものにすることが重要である。
「断捨離(だんしゃり)とは、不要な物を減らし、生活に調和をもたらそうとする思想」1) とある。査察等の際、医薬品製造所の製造室に使用しなくなった設備があると、異物混入や交差汚染の原因となるため、撤去するよう指導される。原材料や資材の場合は、混同防止の観点から、撤去するよう求められる。では、文書の場合はどうだろうか。使用していない文書等の改訂や廃止を行うことは必要である。しかし、廃止した品目のSOPや使用禁止となった設備の操作手順が残っていることはあるだろう。手順書の内容すべてが廃止になることも少ない。倉庫管理手順に保管する品目名を記載していることも多い。しかし、その品目一覧に扱わなくなった品目名の記載が残っていたり、追加しなくてはならない品目名の記載がなかったりすることもある。手順書ごとに対象品目を記載する必要はない。いろいろな手順書とトレースができる品目一覧を別途作成すればよい。製品標準書にその品目で使用するSOPをきちんと記載し、トレースが取れるようにすれば済む問題である。しかし、今までの管理だからと、文書管理の改善が進まない製造所も多い。文書の整理も、断捨離として、ある段階で踏ん切りをつけないと思うように進まない。過去の文書管理と決別することも必要である。
ルールは、その時の状況等で変更されなければならない。ある作業が手順書の記載内容と齟齬があると、逸脱処理するケースは多いと思う。その逸脱は、医薬品の品質に関わるのだろうか、リスク分析が必要である。しかし、文書の改訂を必ず変更管理をする必要はない。変更管理の対象でなければ、リスク分析を行わないことになる。手順書の改訂が、その製造方法や試験方法、管理方法にならないなら、リスク分析は不要である。手順書や記録用紙などの断捨離は、難しいものである。製造や試験の現場の実態と合わせる必要がある。チェックシートなどが現場の負担となっていることも多い。本来、その場で確認すべきチェックを作業終了後のチェックになっている可能性もある。チェックは、現場で必ず確認しなくても、チェック機能が有効なものでなければならない。例えば、清掃記録で、清掃状態を直接、確認せずにチェックする場合、その清掃作業者の普段の清掃方法等を把握しているなら、清掃の作業者をチェックすることで、清掃状況の確認をしたともいえる。その場合、清掃作業のスキルを明確にした教育訓練等の記録がその根拠となる。現場でのチェックをする場合、清掃作業が2人で行うなら、相互に記録者と確認者として、清掃状態の確認をし、記録する方法もある。工程責任者が必ずチェックするのではなく、権限を委譲し、ラインリーダーが現場確認するなど、チェックが有効なものとなるようしなければならない。チェックが必要かどうかも検討し、品質へのリスクがあるかチェック項目を検討してほしい。チェックが形がい化しないようチェックを増やすのではなく、重要なチェックをきちんとチェックした記録としなければならない。無駄で不要なチェックを削減することで、チェックが有効なものにすることが重要である。
2ページ中 1ページ目
コメント
/
/
/
この記事へのコメントはありません。
コメント