離散系シミュレーション利用の勧め【第2回】
2018/03/23
施設・設備・エンジニアリング
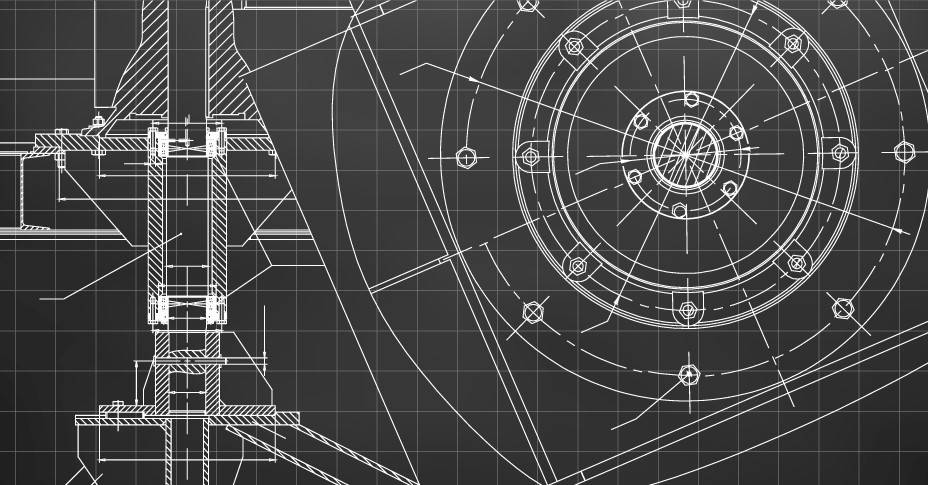
はじめに
前回は、離散系シミュレーションの概要およびその適用分野について説明したが、今回は特に製造業において離散系シミュレーションが具体的にどのような場面で有効に利用されているかについて、比較的簡易な製造プロセスの例を使って説明する。また、医薬品製造業の現状に当てはめた場合の活用方法についても考察する。
1. 製造業における生産システムのモデリング
離散系シミュレーションの柔軟なモデリング機能は、製造業の中でも複雑な製造工程を有し、多くの制約条件を考慮する必要のある工場において、特に威力を発揮する。しかしここでは工場の生産システムのモデリングおよびケーススタディの手順を理解しやすくするため、図1.に示すような比較的簡単な製造プロセスを例にとって説明する。
この製造プロセスでは、共通の基本部品にA,B二種類の部品を組み込むことでA製品とB製品を製造している。組立工程はA製品とB製品で別々の工程となっているが、他の全ての工程はA,B製品共通となっている。例えば、現在はほぼ半々の割合でA製品とB製品を生産しているものの、近い将来A製品の需要が増大してB製品の需要が減少することが見込まれる場合に、どの程度までのアンバランスに対応できそうかを知りたいとすると、まず現状の運転をなるべく忠実に再現するモデルを作成し、その後A製品とB製品の生産割合を段階的に変えてみて、その生産システムに与える影響を推定する必要がある。現状の運転を忠実に再現するためには、現状の運転データに基づいて推定した以下のようなモデルの入力情報をまず準備する。
● 前処理工程の開始時間間隔の分布(見込み生産か受注生産かによって大きく
異なる)
● A製品部品とB製品部品のアベーラビリティ(常に十分な量の在庫があるか)
● 各処理工程の機械台数および処理時間の分布
● 検査工程での不良率
これらの推定値が正しいかどうかは、シミュレーションを実施した結果得られる各工程の利用率や平均待ち時間、平均処理待ち部品数、プロセスのスループット、部品投入から製品完成までの平均滞留時間などを実際の運転実績と比較することで検証できる。一般的に、上記のモデル入力情報を全て正確に推定することは困難なことが多いが、特に重要と目される入力情報の精度の向上に注力することで、より良い結果が期待できる。今回の例で言えば、もし検討の目的をA製品の割合の増大の影響評価に絞るのであれば、組立工程1関連の情報の精度を高めるよう、特に努力すべきであろう。
図2.は、市販の離散系シミュレータ(Simio1))を使って作成した図1.の製造プロセスのモデル(①)、A製品の生産割合を変えた場合のケーススタディ結果(②)、そのグラフ表示(③)、モデルの実行時のアニメーション表示(④)を示したものである。
このスタディの結果の概要を表1.に示す。
表1. A製品の生産割合に関するケーススタディ結果
表からわかるように、A製品の割合が70%(ケース2)程度までであれば、生産システム全体に与える影響は少ないが、それ以上になると組立工程1での基礎部品の待ち台数が急速に増加して、生産システム全体での平均滞留時間も大幅に増加することが予想される。
前回は、離散系シミュレーションの概要およびその適用分野について説明したが、今回は特に製造業において離散系シミュレーションが具体的にどのような場面で有効に利用されているかについて、比較的簡易な製造プロセスの例を使って説明する。また、医薬品製造業の現状に当てはめた場合の活用方法についても考察する。
1. 製造業における生産システムのモデリング
離散系シミュレーションの柔軟なモデリング機能は、製造業の中でも複雑な製造工程を有し、多くの制約条件を考慮する必要のある工場において、特に威力を発揮する。しかしここでは工場の生産システムのモデリングおよびケーススタディの手順を理解しやすくするため、図1.に示すような比較的簡単な製造プロセスを例にとって説明する。
この製造プロセスでは、共通の基本部品にA,B二種類の部品を組み込むことでA製品とB製品を製造している。組立工程はA製品とB製品で別々の工程となっているが、他の全ての工程はA,B製品共通となっている。例えば、現在はほぼ半々の割合でA製品とB製品を生産しているものの、近い将来A製品の需要が増大してB製品の需要が減少することが見込まれる場合に、どの程度までのアンバランスに対応できそうかを知りたいとすると、まず現状の運転をなるべく忠実に再現するモデルを作成し、その後A製品とB製品の生産割合を段階的に変えてみて、その生産システムに与える影響を推定する必要がある。現状の運転を忠実に再現するためには、現状の運転データに基づいて推定した以下のようなモデルの入力情報をまず準備する。
● 前処理工程の開始時間間隔の分布(見込み生産か受注生産かによって大きく
異なる)
● A製品部品とB製品部品のアベーラビリティ(常に十分な量の在庫があるか)
● 各処理工程の機械台数および処理時間の分布
● 検査工程での不良率
これらの推定値が正しいかどうかは、シミュレーションを実施した結果得られる各工程の利用率や平均待ち時間、平均処理待ち部品数、プロセスのスループット、部品投入から製品完成までの平均滞留時間などを実際の運転実績と比較することで検証できる。一般的に、上記のモデル入力情報を全て正確に推定することは困難なことが多いが、特に重要と目される入力情報の精度の向上に注力することで、より良い結果が期待できる。今回の例で言えば、もし検討の目的をA製品の割合の増大の影響評価に絞るのであれば、組立工程1関連の情報の精度を高めるよう、特に努力すべきであろう。
図2.は、市販の離散系シミュレータ(Simio1))を使って作成した図1.の製造プロセスのモデル(①)、A製品の生産割合を変えた場合のケーススタディ結果(②)、そのグラフ表示(③)、モデルの実行時のアニメーション表示(④)を示したものである。
このスタディの結果の概要を表1.に示す。
表1. A製品の生産割合に関するケーススタディ結果
検討ケース | 現状 | ケース1 | ケース2 | ケース3 |
A製品割合 (%) | 50 | 60 | 70 | 80 |
組立工程1利用率(%) | 59.4 | 71.0 | 82.3 | 95.4 |
組立工程1基礎部品 平均待ち台数(-) |
0.24 | 0.46 | 1.42 | 9.36 |
スループット(台/hr) | 3.95 | 3.94 | 3.95 | 3.98 |
平均滞留時間(Hr) | 1.75 | 1.78 | 1.99 | 3.85 |
表からわかるように、A製品の割合が70%(ケース2)程度までであれば、生産システム全体に与える影響は少ないが、それ以上になると組立工程1での基礎部品の待ち台数が急速に増加して、生産システム全体での平均滞留時間も大幅に増加することが予想される。
2ページ中 1ページ目
コメント
/
/
/
この記事へのコメントはありません。
コメント