ゼロベースからの化粧品の品質管理【第37回】
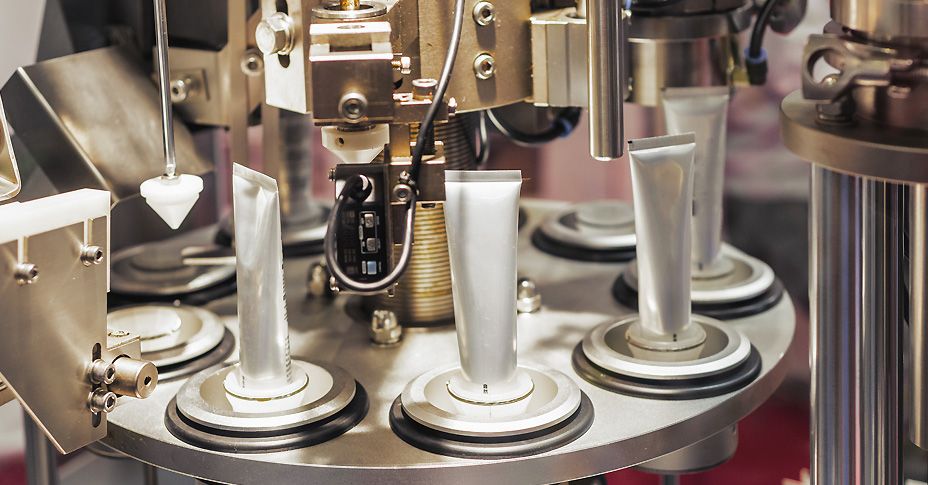
今回は材料トラブルをどのように低減していくのかについて。
―『材料トラブルをどのように低減していくのか』について―
化粧品GMPに関して、具体的な対応策について考え方について、ISOの規格要求事項の解説ではなく実際の運用面から私の経験を喪にお話させて頂いています。今回は、実生産でトラブル発生が多く多くの企業が頭を抱えており、市場回収の中でもトップの発生要因となっている材料関連に関する留意事項についてお話させて頂きます。尚、市場回収事故の要因として材料関係の中でも最も多い発生要因は表示関連の誤りになりますが、この表示関連のトラブル防止は次回として、先ずは材料の管理全般についてお話させて頂きます。
3年間以上の減量保証ができているのか?
熱転写方式における加温温度のバラツキ、印刷後の放置時間と印刷強度のバラツキの確認が行われているのか?
等様々なリスクがあります。しかしながら、材料メーカーでも中味との相互作用はなかなか把握できないため、最終的には製造所が保証しなければなりませんが、製造所も材料に関するリスクはなかなか細かな工程までは把握できないことからリスクの把握、ロット変動のリスクの把握は難しいように感じています。
更に厄介なことに、材料に関しては均質性の概念の適用が難しく、均質性の管理体制をとることが難しく、GMPの要求としても管理単位でロット付けを行うことになっています。そのため、材料関係のトラブルが派生した場合には範囲の特定に一苦労します。発生要因に基づいて均質性の視点から範囲を特定する作業が必要になりますが、構成するパーツや組み込み作業や加飾工程の特定時間帯の処理が不適切だった場合には納入された材料もある程度は固まっていますが、各荷姿の中でばらついて存在することが多く、統計的根拠に基づき範囲を特定することにならざるを得ないケースがあります。可能ならば、個々の材料のトレーサビリティーが追えることが理想ですが、実態は難しいように感じています。
そこで、先ずは材料に関して事前に把握しておくべき事項についてまとめてみました。
QC工程図を入手してリスクの認識とその対策、モニタリングが適正に行われていることを事前に検証する。
先ずは素材の特性と中味に対する保証、使用する場所や使用方法と容器の形状や構造と合致していることが必要です。中味と容器の組合せ保証では、使用するバルクがないと保証が出来ないという話を聞きますが、有機概念図から極性を考えて過酷試験液を作るとか、特定成分を増量して様子を見るとかの方法があります。単純にある特定成分を増量する方法がありますが、液の極性が変わってしまいますので樹脂表面の濡れの状態や膨潤の状況や特定成分の収着性の挙動が変わってしまうケースがありますので、注意が必要です。
FDAの査察等ではロジカルなサンプリング数に基づく検査による保証が求められます。しかしながら、実際の現場ではロジカルに必要とされるサンプル数での試験は、費用面や検査工数面でも実施できないのが現状ではないでしょうか?
更に、外観検査はライン上で全数検査を行っていると説明がされるケースがあります。しかしながら、派遣の外国人の方が作業を行っているライン作業の状態を見ますと、加工作業の対応が目一杯で不具合品や外観異常品を適正に排除することが出来ているのか疑問を感じるケースもあります。とは言うものの、ベテランの作業員の方は微妙なレベルを含めた異常品をライン上で弾き出して保証しているケースも多くありますので複雑です。
その対策として、ライン上で外観等の保証を充実させるためには、事前にリスクアセスメントに基づきリスクの高い事項に特化してライン上の検査を導入することや動体視力や脳の反応に着目して、間違いを探すのではなく合致している前提で全体を見ることで検査感度を高める方法等があります。一歩踏み込んで、仕組みとして体制の工夫が重要と考えます。
ライン作業における発生する可能のあるトラブルについてリスクアセスメントを行い、発生リスクとその対応を準備しておくことが必要です。
例えば、充填作業において瓶口と充填ノズルの接触による瓶口の欠けに対するリスクがあります。この場合には、必ずしも充填後の瓶口の欠けを人の配置で目視確認することや画像センサーで確認を行うことは必ずしもはなく、適切なノズル径の選定とセット完了時点での確認、充填作業の途中での定期的な確認を行うことで保証が出来ると考えます。ある程度は割り切りも必要と考えます。その一方で、栓掛け工程で逆回転の作業を行わない場合には斜め掛けのリスクがありますので、目視確認作業、画像センサーによる確認、高さセンサーによる確認が必要になります。
設計段階では実使用を想定した形で想定される状況に対してバリデートする過酷条件での保証を行うと必要があります。加えて、最終製品検査では外観を中心とした検査と実使用を想定した視点で材料に関する検査を実施しているかと思います。但し、この検査ではバリに関する指辺り等は経時確認は必要ありませんが、ケミカルアタックによるシール部からの漏れや染み出しや容器の変形については経時フォローする体制を整えておくことが重要です。
2ページ中 1ページ目
コメント
/
/
/
この記事へのコメントはありません。
コメント