医薬品のモノづくりの歩み【第28回】
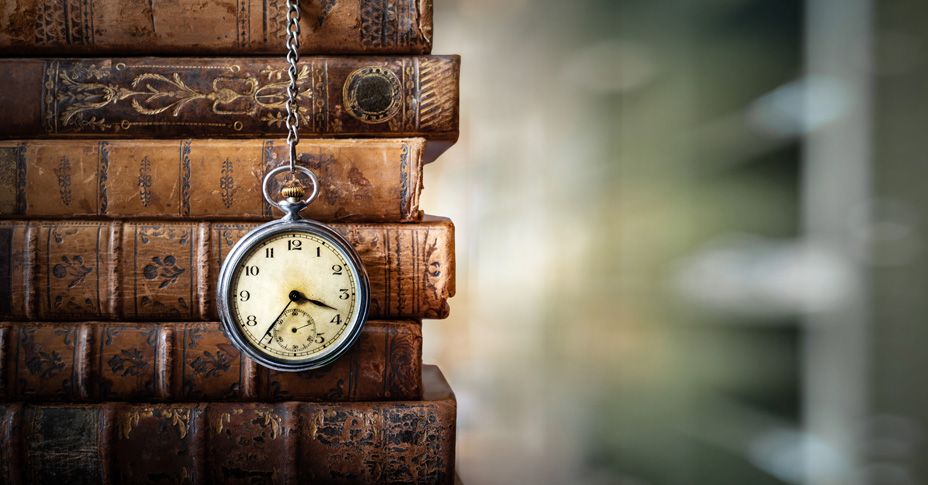
生産性向上の取り組みのステップ3である間接費の削減と原価低減活動について。
「モノづくりカルチャー」と生産性(8)
今回は、工場における生産性向上の取り組みの最後のステップ3である間接費の削減と原価低減活動についてお話しします(図1の赤枠)
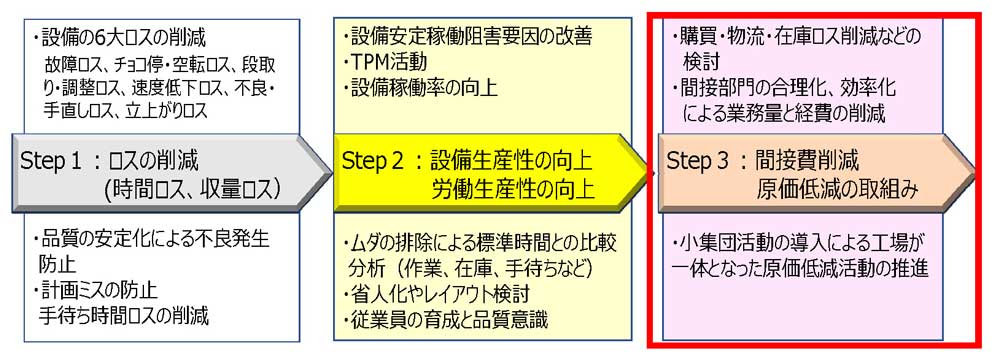
ここでは間接業務の効率化や工場一体となった小集団活動の推進が主な取り組みになります。間接費の削減や原価低減に向けた業務の効率化は、業務の時間的・経済的コストを減らすことにより得られた価値(リソース)を有効活用して、新たなアウトプットを生み出す生産性向上のための重要なステップになります。
多品種少量生産である医薬品の製造では、製造準備作業や洗浄・切替えなど付帯作業が多く発生します。また、製品ごとの専用部品や容器が増えることで、保管スペースの確保が必要になり、生産ラインの狭隘化を招くことがあります。最近では、GMP規制強化に伴い、SOPやドキュメント作成も多く発生しており、このような付帯作業や間接業務に着目して、非効率を招く主な要因を見える化し、その改善に取り組むことが求められてきています。例えば、業務の内容を可視化して、そこで発生しているロスやムダを削減し、マニュアル化します。切替え、洗浄、生産準備など非生産時間である付帯作業では、切替え部品の削減や外段取り化、洗浄の自動化などワークフローの改善に取り組みます。また、IT技術の活用を進め、SOP、記録、報告書類などドキュメント類の電子化とDX活用によるデータ解析や業務プロセスの見直しを図っていくことにも取り組みます。尚、ここでも5Sは、業務の効率化において重要な取り組みの一つになります。
次に、「モノづくり」の基本要素の生産性(Cost)の向上をテーマに取り上げて取り組む小集団活動についてです。この活動は「原価低減活動」と呼ばれ、Q(品質)、D(安定供給)とのバランスを念頭に置いて、全員参加型の活動として取り組みます。この活動を展開するポイントは以下のようなことが挙げられます。
- 問題意識を持って、日頃の業務のムダやロスを可視化して、改善課課題を明確にします。
- あげられた課題を整理して、テーマを決め、誰もが納得できる無理のない目標を設定し共有します。
- 改善が部分最適でなく、モノづくりの基本要素QCDのバランスが取れたものになっていることを確認します。
- 改善の実行では、その内容がSOPの改定など品質に関わる場合、GMPの変更管理の手続きに沿って進めます。
- 改善の結果、目標通りの成果が継続的に得られているか、新たな課題が発生していないかを確認し、更に、成果を定量的に評価するKPIを設定して、成果の見える化を検討します。
2ページ中 1ページ目
コメント
/
/
/
この記事へのコメントはありません。
コメント