GMPヒューマンエラー防止のための文書管理【第35回】
2020/08/07
品質システム
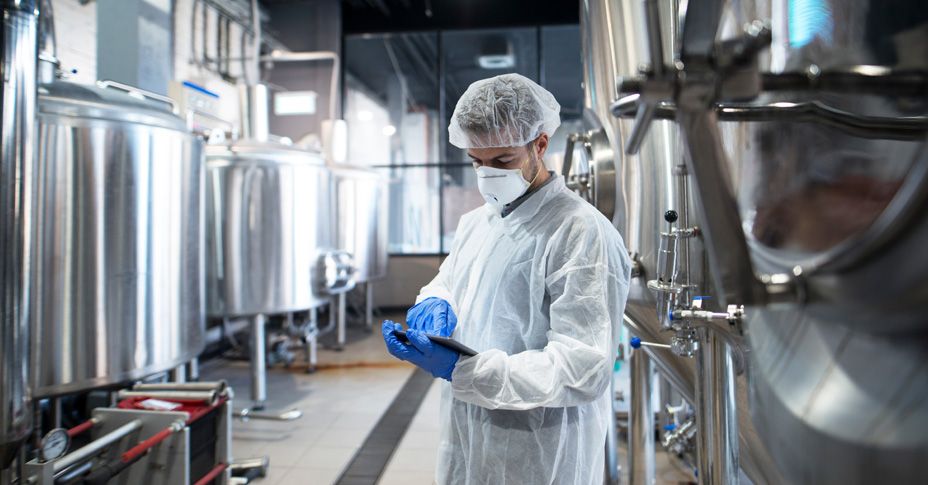
1.完璧
文書の制定や改訂の際、完璧を目指すあまり、結局、手が付けられない製造所は多いと思う。製品標準書を改訂したいが、品目が多くて、すべての品目の製品標準書を改訂できないと、手を付けない製造所もあるだろう。一度にすべての文書を改訂することはない。使う文書から改訂していけばよい。年に1ロットも製造しない品目もあるだろう。その品目の改訂は、使う時までに改訂すれば十分である。文書は使用する段階で、適正な記載がされればよい。
製造方法等の手順書を制定する際、現場の作業者が理解するためと、詳細に記載しすぎることもあると思う。詳細な記載が却って、理解しにくく、ヒューマンエラーを招くこともある。完璧な文書を最初から求めることはない。製造方法ならば、当然、バリデートされる。PQやPVにおいて、期待する結果が得られることを検証するが、その手順に間違いなく実施できることも合わせてみなければならない。PVは、実生産で、作業員がその作業を理解していることを確認することでもある。バリデーションを実生産の作業者と異なるバリデーションの実施部署が行うならば、その作業について、教育訓練をしてからでないと、生産を開始できない。変更管理として、変更開始前に、必要な教育訓練をしなければならない。PVを現場の作業者の教育訓練とする製造所は多い。
手順書は、その作業ができることを検証しなければならない。その作業が実施できない手順書ではあってはならない。手順のとおりに実施できなければ、手順からの逸脱となる。手順を定める時は、リスク分析をし、逸脱が生じないか、作業ができることを検証する必要がある。もし、その後の作業において、ヒューマンエラー等の人為的逸脱、できない作業が発覚した時は、リスク分析が不十分であったこととなる。そのエラーに対して、原因を特定して、その作業を見直すことになる。想定外のリスクが発生したからと責められるものではなく、その是正措置を行うことが重要である。最初から完璧な手順が作成できれば、一番効率的で無駄がない。しかし、実際に実行して、見つかる問題はある。その点をあらかじめ、発見できるようにバリデーションを実施しなくてはならない。また、作業のやりにくい点をあらかじめ見つけるために、教育訓練がある。完璧な手順書を作成できないことから、改革をせず、見直しをせず、放置することがあってはならない。
手順書を作成する時、完璧なものにするつもりはないと思う。しかし、一旦、手順書を制定すると、なかなかルールの改訂ができず、手順の逸脱を恐れ、その手順の意義を理解せずに、いつまでもそのルールに縛られていることも多い。査察時等で、何故、この手順が必要か質問すると、以前からやっているとか、監査で指摘されたからとその手順の意味を理解していないことがあった。例えば、製造記録におけるチェック項目は何のためにチェックするのか、そのチェックがされず、見逃したなら、どんなリスクが生じるのか、品質への影響があるのかを作業者が理解していなければ、完璧な手順とは言えない。GMPの基本は、手順であるルールに従い、そのルールに基づき実行することが基本だが、そのルールの意味を知らなければ、リスクを招く。ルールは、作業者の理解や設備等環境等その時の状況により、その都度、改訂されなければならない。改訂されないルールは、使用されないルールである。
文書の制定や改訂の際、完璧を目指すあまり、結局、手が付けられない製造所は多いと思う。製品標準書を改訂したいが、品目が多くて、すべての品目の製品標準書を改訂できないと、手を付けない製造所もあるだろう。一度にすべての文書を改訂することはない。使う文書から改訂していけばよい。年に1ロットも製造しない品目もあるだろう。その品目の改訂は、使う時までに改訂すれば十分である。文書は使用する段階で、適正な記載がされればよい。
製造方法等の手順書を制定する際、現場の作業者が理解するためと、詳細に記載しすぎることもあると思う。詳細な記載が却って、理解しにくく、ヒューマンエラーを招くこともある。完璧な文書を最初から求めることはない。製造方法ならば、当然、バリデートされる。PQやPVにおいて、期待する結果が得られることを検証するが、その手順に間違いなく実施できることも合わせてみなければならない。PVは、実生産で、作業員がその作業を理解していることを確認することでもある。バリデーションを実生産の作業者と異なるバリデーションの実施部署が行うならば、その作業について、教育訓練をしてからでないと、生産を開始できない。変更管理として、変更開始前に、必要な教育訓練をしなければならない。PVを現場の作業者の教育訓練とする製造所は多い。
手順書は、その作業ができることを検証しなければならない。その作業が実施できない手順書ではあってはならない。手順のとおりに実施できなければ、手順からの逸脱となる。手順を定める時は、リスク分析をし、逸脱が生じないか、作業ができることを検証する必要がある。もし、その後の作業において、ヒューマンエラー等の人為的逸脱、できない作業が発覚した時は、リスク分析が不十分であったこととなる。そのエラーに対して、原因を特定して、その作業を見直すことになる。想定外のリスクが発生したからと責められるものではなく、その是正措置を行うことが重要である。最初から完璧な手順が作成できれば、一番効率的で無駄がない。しかし、実際に実行して、見つかる問題はある。その点をあらかじめ、発見できるようにバリデーションを実施しなくてはならない。また、作業のやりにくい点をあらかじめ見つけるために、教育訓練がある。完璧な手順書を作成できないことから、改革をせず、見直しをせず、放置することがあってはならない。
手順書を作成する時、完璧なものにするつもりはないと思う。しかし、一旦、手順書を制定すると、なかなかルールの改訂ができず、手順の逸脱を恐れ、その手順の意義を理解せずに、いつまでもそのルールに縛られていることも多い。査察時等で、何故、この手順が必要か質問すると、以前からやっているとか、監査で指摘されたからとその手順の意味を理解していないことがあった。例えば、製造記録におけるチェック項目は何のためにチェックするのか、そのチェックがされず、見逃したなら、どんなリスクが生じるのか、品質への影響があるのかを作業者が理解していなければ、完璧な手順とは言えない。GMPの基本は、手順であるルールに従い、そのルールに基づき実行することが基本だが、そのルールの意味を知らなければ、リスクを招く。ルールは、作業者の理解や設備等環境等その時の状況により、その都度、改訂されなければならない。改訂されないルールは、使用されないルールである。
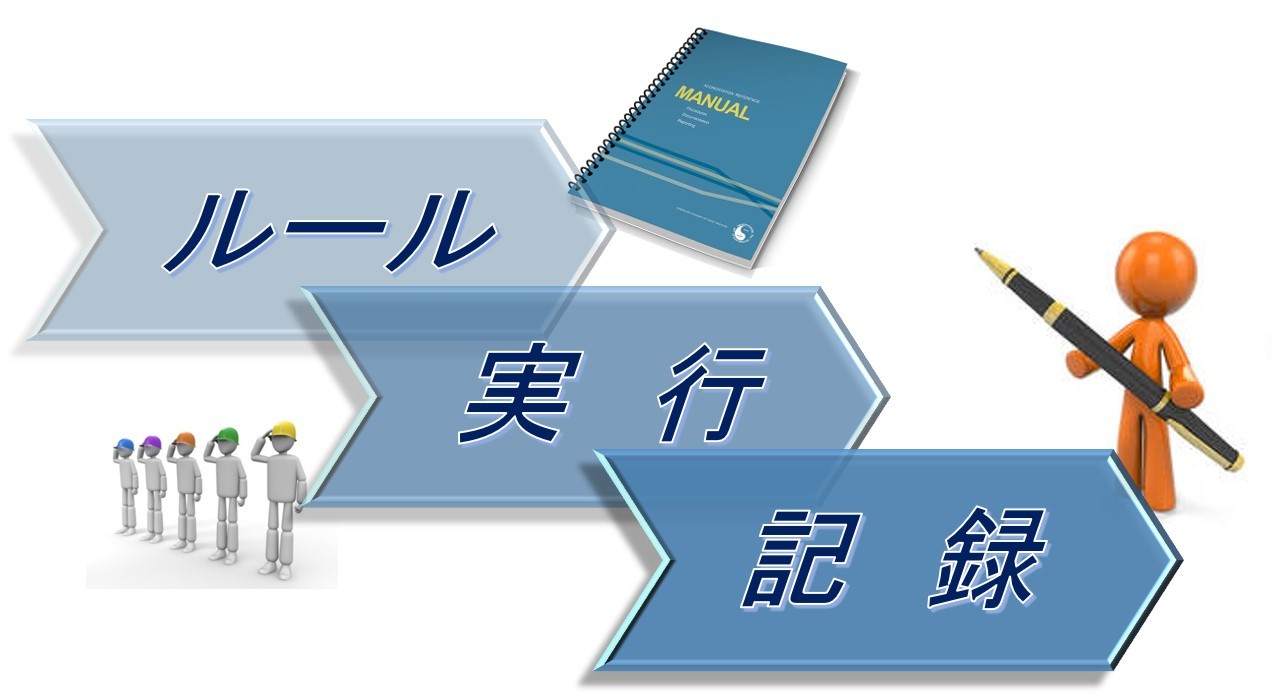
2ページ中 1ページ目
コメント
/
/
/
この記事へのコメントはありません。
コメント